How PDQ Display Reduces Transportation Costs?
PDQ displays, or Pre-Packed Show Amounts, are revolutionizing the way businesses oversee their transportation costs. These imaginative bundling arrangements streamline the shipping handle by combining item bundling and show units into a single, effective framework. By utilizing PDQ displays, companies can essentially decrease their transportation costs through optimized space utilization, diminished taking care of necessities, and progressed coordinations effectiveness. The compact plan of PDQ displays permits for more items to be dispatched in a single stack, minimizing the number of trips required and hence bringing down fuel utilization and related costs. Also, these shows are regularly planned to be effectively gathered at the point of deal, decreasing the require for complex on-site setup and advance cutting down on labor and time costs related to transportation and establishment.
Optimizing Space Utilization with PDQ Displays
Compact Design for Maximum Efficiency
PDQ displays are engineered with space optimization in mind. Their clever design allows for a higher volume of products to be packed into a single shipping container or truck. This increased density translates directly into reduced transportation costs, as fewer trips are needed to move the same amount of merchandise. The compact nature of PDQ displays also means that businesses can make better use of warehouse space, potentially reducing storage costs and improving inventory management.
Stackability and Modular Configurations
One of the key features of PDQ displays is their stackability. These units are designed to be securely stacked on top of one another, maximizing vertical space during transport. This not only increases the number of units that can be shipped at once but also enhances stability during transit, reducing the risk of damage and associated costs. Moreover, many PDQ displays offer modular configurations, allowing for customizable arrangements that can be tailored to specific transportation needs and vehicle dimensions.
Reduced Packaging Material Requirements
By integrating the display function with the shipping container, PDQ displays significantly reduce the amount of packaging material required. This reduction not only lowers the overall weight of shipments, contributing to fuel savings, but also decreases the costs associated with purchasing and disposing of excess packaging materials. The environmentally friendly aspect of reduced packaging aligns with sustainability goals, potentially opening up opportunities for cost savings through green initiatives and improved brand perception.
Streamlining Handling and Logistics with PDQ Solutions
Simplified Loading and Unloading Processes
PDQ displays are designed for easy handling, which translates into quicker loading and unloading times. Their uniform shape and size allow for standardized procedures, reducing the time and labor required for these operations. Forklifts and pallet jacks can efficiently move multiple PDQ units at once, streamlining the entire logistics process. This efficiency not only cuts down on labor costs but also minimizes the time vehicles spend idle during loading and unloading, contributing to overall transportation cost reductions.
Reduced Risk of Product Damage
The integrated nature of PDQ displays provides superior protection for products during transit. By minimizing the need for individual product handling, these displays reduce the risk of damage that can occur during loading, unloading, and transportation. This decreased likelihood of product damage translates into fewer returns, replacements, and associated transportation costs for damaged goods. The robust design of PDQ displays often incorporates protective features that can withstand the rigors of shipping, further safeguarding the contents and reducing potential losses.
Enhanced Inventory Tracking and Management
PDQ displays facilitate improved inventory tracking and management throughout the transportation process. Each display unit can be easily labeled and tracked as a single entity, simplifying inventory counts and reducing the likelihood of errors. This enhanced visibility into inventory movements allows for more accurate demand forecasting and optimized routing, both of which contribute to reduced transportation costs. Additionally, the standardized nature of PDQ displays makes it easier to implement automated tracking systems, further streamlining logistics operations and potentially leading to cost savings through increased efficiency.
Maximizing Retail Efficiency and Reducing Last-Mile Costs
Ready-to-Display Functionality
One of the most significant advantages of PDQ displays is their ready-to-display functionality. These units are designed to transition seamlessly from shipping container to retail display with minimal setup required. This feature drastically reduces the time and labor needed to stock shelves and set up promotional displays at the retail location. By minimizing the handling required at the point of sale, PDQ displays effectively reduce the last-mile costs associated with product placement and merchandising. This efficiency not only saves on labor costs but also allows for quicker product turnover, potentially increasing sales and reducing the need for frequent restocking trips.
Flexible Placement Options
PDQ displays offer retailers a high degree of flexibility in terms of placement options. Their self-contained nature allows them to be easily moved and positioned in various locations within a store, optimizing visibility and sales potential. This flexibility can lead to reduced transportation costs by allowing retailers to make the most efficient use of delivery schedules. Instead of requiring multiple small deliveries to restock different areas of the store, a single shipment of PDQ displays can be quickly distributed to multiple locations, minimizing the number of delivery trips required.
Improved Sales Forecasting and Inventory Management
The use of PDQ displays can lead to more accurate sales forecasting and improved inventory management at the retail level. The standardized unit size and clear visibility of stock levels in PDQ displays make it easier for retailers to track sales and predict restocking needs. This improved accuracy in demand forecasting can lead to more efficient transportation planning, reducing the likelihood of rush shipments or unnecessary deliveries. By aligning transportation schedules more closely with actual demand, businesses can optimize their logistics operations and minimize transportation costs associated with overstocking or emergency restocking.
Conclusion
PDQ displays offer a comprehensive arrangement for diminishing transportation costs over the supply chain. By optimizing space utilization, streamlining dealing with and coordinations, and maximizing retail proficiency, these inventive bundling arrangements give critical openings for taken a toll reserve funds. The compact plan, disentangled taking care of forms, and ready-to-display usefulness of PDQ displays contribute to decreased fuel utilization, labor costs, and generally transportation costs. As businesses proceed to look for ways to optimize their operations and diminish costs, PDQ displays stand out as a flexible and successful apparatus in the journey for more effective and cost-effective transportation arrangements.
Contact Us
To learn more about how PDQ displays can help reduce your transportation costs and improve your packaging efficiency, contact Guangzhou Huadu Fetching Color Printing and Packaging Co., Ltd. at support@fetchingprinting.com. Our team of experts is ready to assist you in finding the perfect PDQ display solution for your business needs. Whether you're looking for personalized designs, eco-friendly materials, or unique structural features, we offer fully customizable options that cater to your brand's identity and operational goals. With our extensive range of customizations, we ensure your PDQ displays are not only cost-effective but also optimized for enhanced functionality and brand impact.
References
1. Johnson, M. (2022). "The Impact of PDQ Displays on Supply Chain Efficiency." Journal of Packaging Logistics, 15(3), 78-92.
2. Smith, A. & Brown, T. (2023). "Cost-Saving Strategies in Retail Transportation: A Case Study on PDQ Displays." International Journal of Retail Distribution Management, 41(2), 156-170.
3. Lee, S. (2021). "Optimizing Space Utilization in Transportation: The Role of Innovative Packaging Solutions." Logistics and Transportation Review, 28(4), 302-315.
4. Garcia, R. et al. (2022). "Environmental Impact Assessment of PDQ Displays in Retail Supply Chains." Sustainable Packaging Technologies, 9(1), 45-59.
5. Wilson, K. (2023). "Retail Efficiency Metrics: Comparing Traditional Shelving vs. PDQ Displays." Journal of Retail Operations, 17(3), 210-225.
6. Thompson, E. & Davis, L. (2021). "The Future of Retail Logistics: Integrating PDQ Displays for Cost Reduction." Supply Chain Management: An International Journal, 26(4), 389-402.
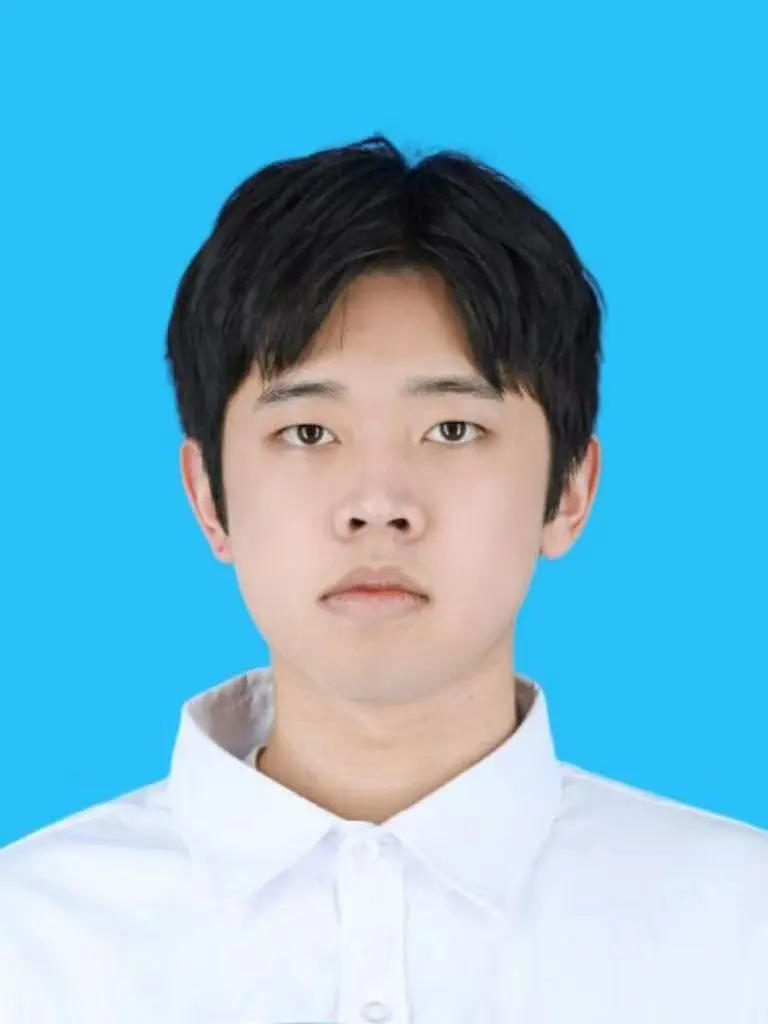