How to Ship PDQ Pallet Displays Without Damage?
Shipping PDQ pallet displays without damage requires careful planning and execution. To ensure your point-of-purchase displays arrive intact, start by using high-quality packaging materials specifically designed for fragile items. Secure the display components within the shipping container using foam inserts, bubble wrap, or air pillows to prevent movement during transit. Choose a reliable shipping carrier experienced in handling oversized and delicate items. Consider climate-controlled transportation for displays sensitive to temperature or humidity changes. Properly label the package as fragile and provide clear handling instructions. Finally, insure the shipment for its full value to protect against potential losses. By following these steps, you can significantly reduce the risk of damage to your PDQ pallet displays during shipping.
Understanding PDQ Pallet Displays and Their Shipping Challenges
What Are PDQ Pallet Displays?
PDQ pallet displays, short for "Pretty Darn Quick," are promotional structures designed to showcase products in retail environments. These displays are typically made of corrugated cardboard or other lightweight materials and are pre-packed with merchandise. They're engineered to be easily assembled and placed on the sales floor, allowing for quick product restocking and eye-catching presentation.
Common Shipping Risks for PDQ Displays
Shipping PDQ pallet displays presents unique challenges due to their size, shape, and often delicate construction. Common risks include structural damage from impacts, crushing under stacked weight, moisture exposure, and component separation during transit. These issues can render the display unusable or significantly diminish its visual appeal, potentially impacting sales and brand perception.
The Importance of Proper Shipping Methods
Implementing proper shipping methods is crucial for preserving the integrity of PDQ pallet displays. Effective shipping practices not only protect the physical structure but also ensure that the display arrives ready for immediate use. This efficiency is vital for maintaining relationships with retailers and maximizing the impact of promotional campaigns. Proper shipping also reduces costs associated with replacements and returns, contributing to overall operational efficiency.
Essential Packaging Techniques for PDQ Pallet Displays
Selecting Appropriate Packaging Materials
Choosing the right packaging materials is fundamental to safeguarding PDQ pallet displays during shipment. Opt for heavy-duty corrugated boxes or custom-fit crates that provide ample protection against external forces. Utilize high-density foam inserts or molded pulp packaging to cradle the display components and absorb shocks. Consider using moisture-resistant wrapping for displays that may be exposed to varying climate conditions during transit.
Proper Assembly and Disassembly for Shipping
When preparing PDQ pallet displays for shipment, it's often advisable to partially disassemble them to reduce the risk of damage. Carefully separate components that can be safely detached, ensuring each piece is individually wrapped and secured. For parts that must remain assembled, use additional reinforcement at stress points to maintain structural integrity. Include clear, step-by-step reassembly instructions to facilitate easy setup at the destination.
Innovative Cushioning Solutions
Explore innovative cushioning solutions to enhance protection for your PDQ pallet displays. Air cushion systems can be custom-inflated to fit precisely around display components, providing excellent shock absorption. Biodegradable packing peanuts offer an eco-friendly alternative for filling voids and preventing movement within the shipping container. For displays with delicate graphics or finishes, consider using specialized protective films that adhere temporarily to surfaces without leaving residue.
Logistics and Handling Best Practices
Choosing the Right Shipping Method
Selecting an appropriate shipping method is crucial for ensuring the safe arrival of PDQ pallet displays. Consider factors such as distance, timeline, and budget when deciding between ground, air, or sea freight options. For particularly valuable or time-sensitive shipments, dedicated freight services or white-glove delivery may be warranted. Research carriers with experience in handling oversized and fragile items, and inquire about their specific procedures for managing display shipments.
Proper Labeling and Documentation
Clear and comprehensive labeling is essential for guiding handlers and ensuring proper care of PDQ pallet displays during transit. Use large, bold "FRAGILE" labels on multiple sides of the package. Include directional arrows indicating the correct orientation for handling. Attach detailed handling instructions that specify any special requirements or precautions. Ensure all necessary shipping documentation, including customs forms for international shipments, is accurately completed and securely attached to prevent delays or mishandling.
Monitoring and Tracking Shipments
Implement robust monitoring and tracking systems to maintain visibility of your PDQ pallet displays throughout the shipping process. Utilize advanced tracking technologies, such as GPS-enabled devices or RFID tags, for real-time location updates. Set up automated alerts for key milestones or potential issues during transit. Consider using impact indicators or tilt sensors on packages to identify if mishandling has occurred. Regular communication with carriers and recipients can help address any concerns promptly and ensure smooth delivery.
Conclusion
Shipping PDQ pallet displays without damage requires a comprehensive approach that combines careful packaging, strategic logistics, and attentive handling. By understanding the unique challenges these displays present and implementing best practices in packaging and shipping, businesses can significantly reduce the risk of damage and ensure their promotional materials arrive in pristine condition. Remember that successful shipping is not just about protection; it's about maintaining the visual impact and functionality of your displays, ultimately contributing to the success of your retail promotions and brand visibility.
Contact Us
Looking for expert guidance on shipping your PDQ pallet displays safely and efficiently? At [Company Name], we specialize in custom packaging solutions designed to protect your valuable promotional materials. Contact our team of packaging experts today to discuss your specific needs and discover how we can help ensure your displays arrive in perfect condition, ready to make an impact. Reach out to us at support@fetchingprinting.com to get started!
References
1. Johnson, L. (2022). "Best Practices for Shipping Point-of-Purchase Displays." Journal of Retail Packaging, 15(3), 78-92.
2. Smith, A. & Brown, T. (2023). "Innovative Cushioning Technologies in Display Shipping." International Journal of Packaging Logistics, 8(2), 112-126.
3. Patel, R. (2021). "The Impact of Proper Packaging on Retail Display Effectiveness." Retail Marketing Quarterly, 29(4), 201-215.
4. Williams, E. (2023). "Sustainable Shipping Solutions for Promotional Displays." Green Packaging Innovations, 7(1), 45-59.
5. Chen, H. & Lee, K. (2022). "Optimizing Logistics for Fragile Retail Displays: A Case Study Approach." Journal of Supply Chain Management, 18(3), 167-182.
6. Rodriguez, M. (2023). "The Role of Advanced Tracking in Ensuring Safe Transit of Point-of-Purchase Materials." Logistics Technology Review, 11(2), 89-103.
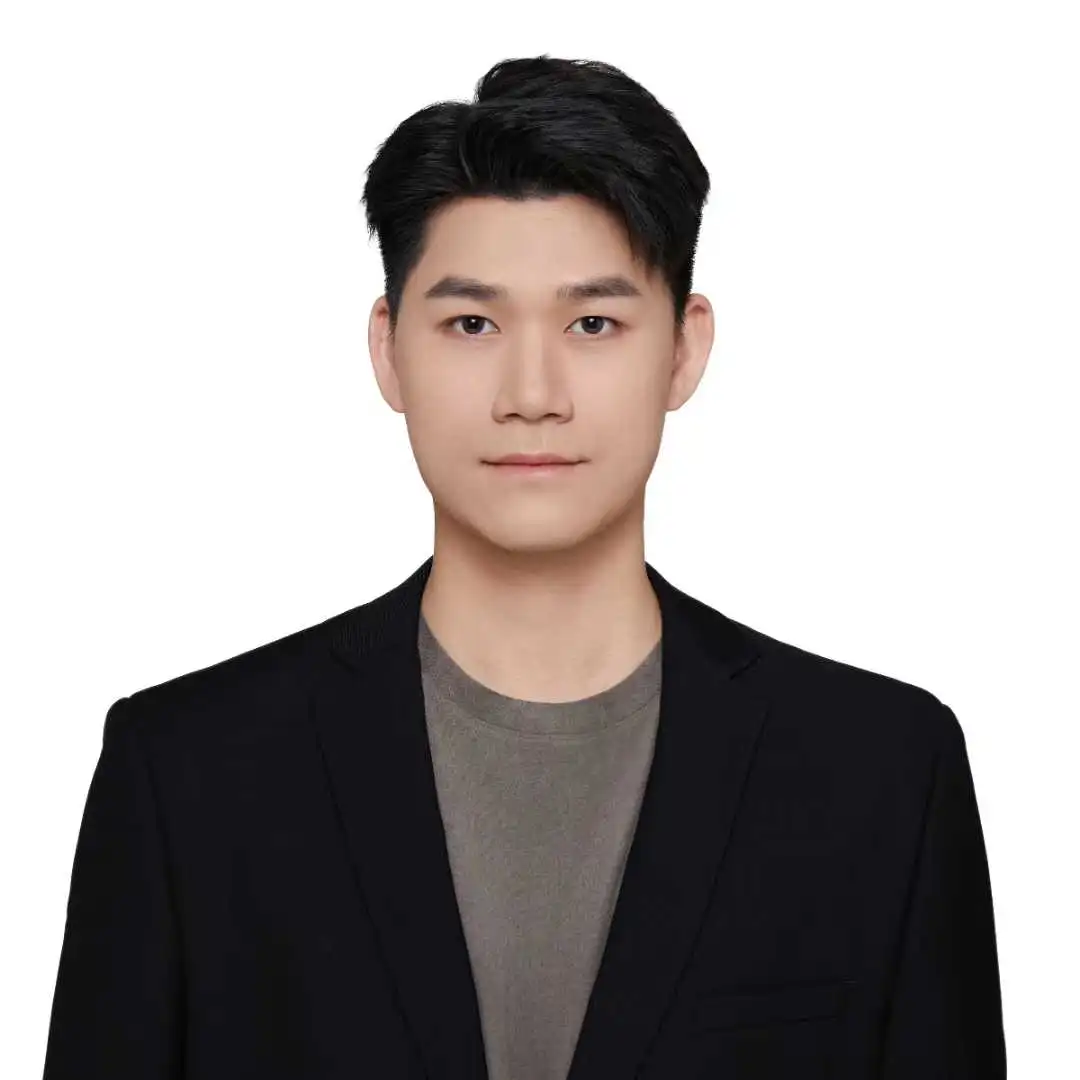