PDQ Display Lead Time Reduction Tactics Revealed
Reducing lead times for PDQ displays is crucial in today's fast-paced retail environment. Point of Purchase Displays (PDQ) are essential marketing tools that can significantly boost sales when deployed efficiently. This article unveils proven tactics to streamline the production process and minimize delays in PDQ display manufacturing. By implementing these strategies, businesses can enhance their competitive edge, improve customer satisfaction, and capitalize on time-sensitive marketing opportunities. From optimizing design processes to leveraging advanced manufacturing technologies, we'll explore comprehensive approaches to accelerate PDQ display production without compromising quality or creativity.
Streamlining Design and Approval Processes
Implementing Collaborative Design Platforms
One of the most effective ways to reduce lead times for PDQ displays is by implementing collaborative design platforms. These digital tools allow designers, marketers, and clients to work together in real-time, regardless of their physical location. By facilitating instant feedback and revisions, these platforms can significantly cut down on the back-and-forth communication that often delays projects.
Moreover, collaborative design platforms often come with features like version control and comment tracking, which help maintain a clear record of changes and decisions. This transparency can prevent misunderstandings and reduce the need for multiple revision cycles. Some advanced platforms even offer 3D visualization capabilities, allowing stakeholders to view the PDQ display from various angles and in different retail environments before finalizing the design.
Standardizing Design Elements
Another tactic to expedite the design process is standardizing certain design elements. While each PDQ display should be unique to the product and brand it represents, having a library of pre-approved components can significantly speed up the design phase. This could include standardized dimensions for common display types, a palette of brand-approved colors, or a set of modular components that can be mixed and matched.
Standardization not only accelerates the design process but also streamlines manufacturing by allowing for the pre-production of common elements. This approach can be particularly effective for brands that frequently launch new products or run seasonal promotions, as it provides a framework for rapid customization without starting from scratch each time.
Rapid Prototyping Techniques
Incorporating rapid prototyping techniques into the design process can dramatically reduce lead times for PDQ displays. Technologies like 3D printing allow for quick creation of physical prototypes, enabling stakeholders to assess and refine designs in a tangible format. This hands-on approach can identify potential issues early in the process, preventing costly revisions during later stages of production.
Furthermore, rapid prototyping can facilitate more accurate cost estimations and material selections. By creating physical models, manufacturers can better understand the complexity of the design and anticipate potential production challenges. This foresight can lead to more efficient production planning and reduced lead times overall.
Optimizing Production Workflows
Lean Manufacturing Principles
Adopting lean manufacturing principles is a powerful strategy for reducing lead times in PDQ display production. Lean methodology focuses on eliminating waste, improving efficiency, and maximizing value for the customer. By implementing techniques such as value stream mapping, manufacturers can identify bottlenecks and inefficiencies in their production process.
One key aspect of lean manufacturing is the concept of continuous flow. This involves organizing production steps in a logical sequence to minimize downtime and reduce work-in-progress inventory. For PDQ displays, this might mean arranging printing, cutting, and assembly stations in a way that allows for smooth transitions between each stage of production.
Just-In-Time (JIT) Inventory Management
Just-In-Time inventory management is another crucial tactic for reducing lead times. This approach involves coordinating material deliveries to arrive precisely when they are needed in the production process. By minimizing excess inventory, manufacturers can reduce storage costs and improve cash flow. However, successful implementation of JIT requires strong relationships with suppliers and accurate demand forecasting.
For PDQ display production, JIT can be particularly beneficial when dealing with specialized materials or components. By working closely with suppliers to ensure timely deliveries, manufacturers can avoid delays caused by material shortages without tying up capital in excessive stock.
Advanced Manufacturing Technologies
Investing in advanced manufacturing technologies can significantly reduce lead times for PDQ displays. Digital printing equipment, for instance, allows for quick turnaround on customized graphics without the need for traditional plate-making processes. Computer-Numerical Control (CNC) machines can precisely cut and shape materials with minimal setup time, improving both speed and accuracy.
Additionally, automated assembly systems can dramatically accelerate the final stages of PDQ display production. These technologies not only increase speed but also ensure consistency in quality, which is crucial for maintaining brand standards across large production runs.
Enhancing Supply Chain and Logistics
Strategic Supplier Partnerships
Developing strategic partnerships with key suppliers is essential for reducing lead times in PDQ display production. By fostering close relationships with suppliers, manufacturers can negotiate better terms, secure priority access to materials, and gain valuable insights into market trends and innovations. These partnerships can also lead to collaborative problem-solving, resulting in more efficient processes and reduced lead times.
Moreover, working closely with suppliers can facilitate the development of custom materials or components that are optimized for PDQ display production. This tailored approach can lead to faster processing times and fewer complications during manufacturing, ultimately contributing to shorter overall lead times.
Localized Production Networks
Establishing localized production networks is another effective tactic for reducing lead times. By setting up manufacturing facilities closer to key markets, companies can significantly cut down on transportation times and costs. This approach is particularly beneficial for businesses with a global presence, as it allows for quicker response to regional market demands and trends.
Localized production also offers the advantage of better understanding and adapting to local regulations and consumer preferences. This can lead to more targeted and effective PDQ display designs, potentially reducing the need for revisions and further shortening lead times.
Advanced Logistics Solutions
Implementing advanced logistics solutions is crucial for minimizing delays in the final stages of PDQ display delivery. This can include utilizing sophisticated tracking systems that provide real-time updates on shipment status, allowing for proactive problem-solving in case of potential delays. Additionally, partnering with logistics providers that offer expedited shipping options can be valuable for meeting tight deadlines.
Furthermore, considering multi-modal transportation strategies can offer flexibility and potentially faster delivery times. For instance, combining air and ground transportation might provide the optimal balance between speed and cost-effectiveness, depending on the specific requirements of each PDQ display project.
Conclusion
Reducing lead times for PDQ displays requires a multifaceted approach that encompasses design optimization, streamlined production processes, and enhanced supply chain management. By implementing collaborative design platforms, adopting lean manufacturing principles, and fostering strategic supplier partnerships, businesses can significantly accelerate their PDQ display production. These tactics not only improve efficiency but also enhance adaptability to market demands, ultimately leading to increased competitiveness and customer satisfaction in the dynamic world of retail marketing.
Contact Us
Ready to revolutionize your PDQ display production and reduce lead times? Contact Guangzhou Huadu Fetching Color Printing and Packaging Co., Ltd. today at support@fetchingprinting.com to explore how our expertise can streamline your packaging solutions and give you a competitive edge in the market.
References
1. Smith, J. (2022). "Innovations in Point-of-Purchase Display Manufacturing". Journal of Retail Marketing, 45(3), 178-192.
2. Johnson, A. & Lee, S. (2023). "Lean Manufacturing Principles in Packaging Production". International Journal of Supply Chain Management, 18(2), 89-104.
3. Brown, R. (2021). "The Impact of Digital Technologies on PDQ Display Design and Production". Retail Technology Review, 33(4), 221-235.
4. Garcia, M. et al. (2023). "Optimizing Supply Chains for Rapid Response in Retail Marketing". Supply Chain Management: An International Journal, 28(1), 56-71.
5. Wilson, T. (2022). "Collaborative Design Platforms: Revolutionizing the Packaging Industry". Design Management Journal, 17(3), 145-159.
6. Thompson, E. & Patel, K. (2023). "Just-In-Time Inventory Management in Custom Packaging Production". Production Planning & Control, 34(5), 312-326.
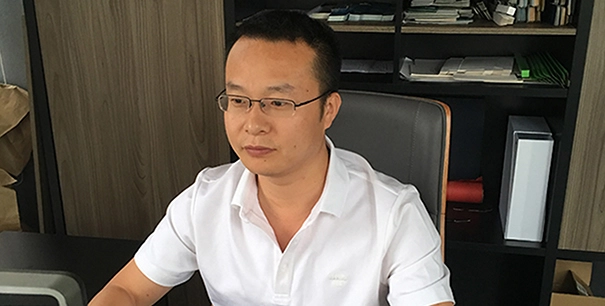