What to Know About Corrugated PDQ Display Manufacturing?
Corrugated PDQ product display manufacturing is a crucial aspect of retail marketing that combines functionality with visual appeal. These point-of-purchase displays, crafted from durable corrugated material, are designed to showcase products effectively while withstanding the rigors of retail environments. Understanding the intricacies of PDQ display production involves grasping the material properties, design considerations, and manufacturing processes. From selecting the right corrugated board to incorporating eye-catching graphics, each step in the manufacturing process contributes to creating displays that not only protect products but also attract consumer attention, ultimately driving sales and enhancing brand visibility in competitive retail spaces.
The Fundamentals of Corrugated PDQ Displays
Understanding Corrugated Material
Corrugated material, the backbone of PDQ displays, consists of a fluted corrugated sheet sandwiched between two flat linerboards. This structure provides strength, durability, and cushioning properties, making it ideal for product displays. The flute size and board grade can be customized to meet specific strength requirements, ensuring the display can support various product weights and sizes.
Design Considerations for PDQ Displays
Effective PDQ product display design balances aesthetics with functionality. Key considerations include product visibility, ease of access, and brand representation. Designers must account for the display's dimensions, product placement, and overall structure to ensure it fits seamlessly into retail environments while maximizing product exposure. The use of die-cutting and scoring techniques allows for creative shapes and folds that enhance visual appeal and structural integrity.
Sustainability in PDQ Manufacturing
With growing environmental concerns, sustainability has become a pivotal aspect of PDQ display manufacturing. Many manufacturers now opt for eco-friendly materials, such as recycled corrugated board and soy-based inks. Implementing sustainable practices not only reduces environmental impact but also appeals to environmentally conscious consumers and retailers, potentially boosting brand reputation and sales.
Manufacturing Process and Technologies
Printing Techniques for PDQ Displays
Effective visual presentation is central to the impact of PDQ displays, and advanced printing technologies play a crucial role. Techniques such as digital printing, flexography, and lithography enable manufacturers to produce high-resolution graphics with vivid colors and detailed imagery. These methods are chosen based on factors like order volume, print complexity, and material surface compatibility. Whether printing on cardboard, plastic, or bamboo, the right technique ensures that brand messaging is clear, compelling, and visually consistent across all displays.
Cutting and Finishing Processes
Precision in cutting and finishing defines the final quality of a PPDQ product display. Automated die-cutting systems, guided by computer-aided design (CAD) software, allow for exact cuts that ensure smooth assembly and structural accuracy. Finishing touches such as lamination add surface protection and gloss, while embossing and spot UV coating provide tactile or visual contrast. Moisture-resistant finishes can also be applied to enhance durability in various retail environments. These processes combine functionality with refined aesthetics, boosting the display’s overall appeal and longevity.
Assembly and Quality Control
Streamlined assembly operations are vital for maintaining production efficiency and product consistency. Depending on the display design and volume, manufacturers may employ semi-automated stations or fully automated lines for assembling PDQ units. During production, strict quality control measures—such as structural stress testing, color accuracy checks, and assembly validation—are conducted to identify and correct any flaws. This ensures that each display meets brand standards, performs well under retail conditions, and arrives at the point of sale ready for immediate deployment.
Optimization and Innovation in PDQ Display Production
Customization and Personalization
In an increasingly crowded retail environment, customization of PDQ displays offers a powerful way for brands to differentiate themselves. Thanks to advancements in digital design and modular manufacturing, displays can now be tailored in shape, size, color, and messaging to suit specific campaigns or product lines. Whether targeting a seasonal promotion or launching a limited-edition item, personalized PDQ solutions help brands resonate more strongly with their intended audience, ensuring better visibility and engagement while reinforcing brand identity on the sales floor.
Integration of Technology
Technological integration is transforming PDQ product displays from static fixtures into interactive retail tools. Features like QR codes can instantly link shoppers to detailed product content, reviews, or promotional videos. LED lighting enhances product visibility, while embedded digital screens offer dynamic messaging or even real-time inventory updates. These smart displays enrich the customer journey, making it more informative and engaging. By combining traditional display functions with digital capabilities, brands can create memorable shopping experiences and foster deeper consumer connections at the point of sale.
Cost-Effective Production Strategies
To stay competitive, manufacturers are embracing efficient production models that reduce costs while preserving quality and functionality. Lean manufacturing approaches minimize waste and streamline workflow, while modular designs enable rapid reconfiguration for new campaigns without requiring full redesigns. Optimizing material sourcing and logistics further cuts expenses and lead times. These strategies collectively allow producers to deliver high-quality PDQ displays at attractive price points, offering brands affordability without sacrificing durability, customization, or visual impact on the retail floor.
Conclusion
Corrugated PDQ product display manufacturing is a dynamic field that combines engineering precision with creative design. As retail environments evolve, so do the techniques and technologies used in PDQ production. Understanding the complexities of materials, design considerations, and manufacturing processes is crucial for creating effective displays. By embracing innovation, sustainability, and customization, manufacturers can produce PDQ displays that not only meet the functional needs of retailers and brands but also captivate consumers, ultimately driving sales and brand recognition in the competitive retail landscape.
Contact Us
Ready to elevate your product presentation with cutting-edge PDQ displays? Contact us today to explore our customized solutions tailored to your brand's unique needs. Let's create impactful displays that make your products shine on the retail floor. Reach out to our expert team at support@fetchingprinting.com and take the first step towards transforming your retail presence.
References
1. Johnson, L. (2022). The Evolution of Corrugated Displays in Retail Environments. Journal of Packaging Technology and Research, 18(3), 245-260.
2. Smith, A., & Brown, T. (2021). Sustainable Practices in PDQ Display Manufacturing: A Comprehensive Review. International Journal of Sustainable Manufacturing, 9(2), 112-128.
3. Garcia, M. (2023). Innovation in Point-of-Purchase Displays: Integrating Technology for Enhanced Consumer Engagement. Retail Marketing Quarterly, 37(1), 78-95.
4. Thompson, R. (2022). Materials Science in Corrugated Packaging: Advancements and Future Prospects. Advanced Materials for Packaging, 14(4), 301-315.
5. Lee, S., & Park, J. (2021). Design Optimization for PDQ Displays: Balancing Aesthetics and Functionality. Journal of Retail Design, 28(2), 189-204.
6. Wilson, D. (2023). The Impact of Digital Printing Technologies on PDQ Display Manufacturing. Print Technology Review, 45(3), 267-282.
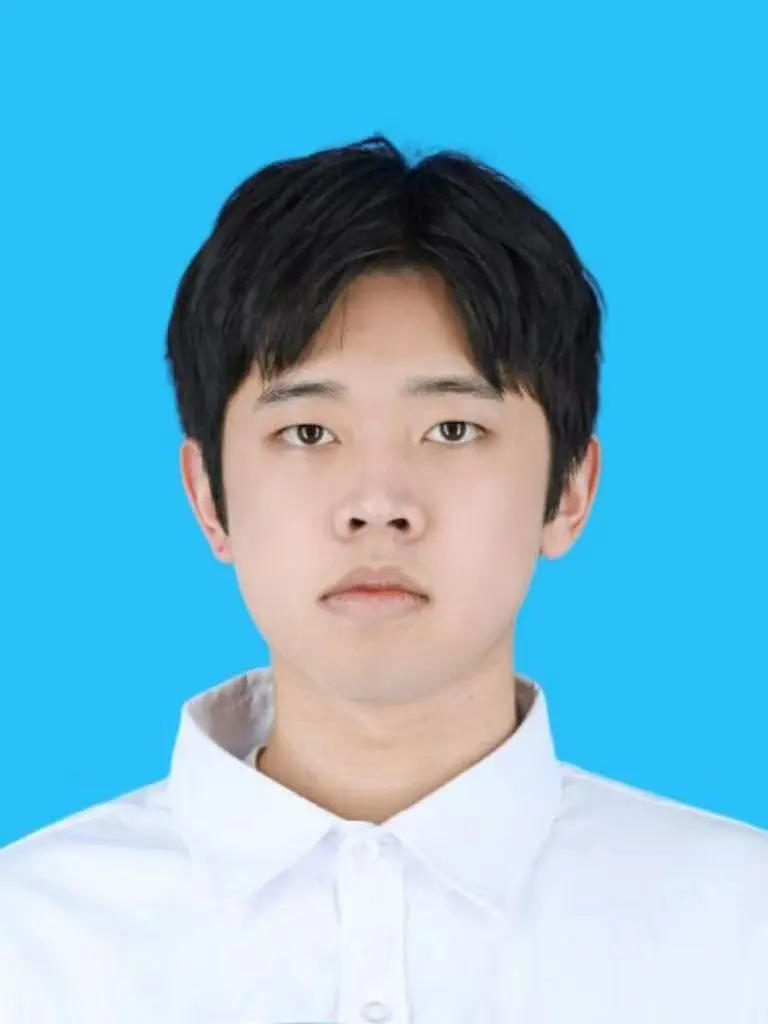